Il faut toute une équipe de techniciens chevronnés pour mener à bien un projet tel que CoroDrill DS20, et il aura fallu presque sept ans pour que les développeurs soient satisfaits et acceptent de lancer sur le marché le plus long et le plus fiable des forets à plaquettes indexables aujourd'hui disponibles.
Un foret qui n'est pas un simple foret à plaquettes indexables, car cet outil peut forer des trous d'une profondeur de sept fois son diamètre en une seule passe sans déflexion et sans surchauffe. Il y a sept ans, quand Sandvik Coromant a commencé à réfléchir à la possibilité de fabriquer un foret à plaquettes indexables pour une profondeur de perçage de 7xD, le premier de ce type sur le marché, personne ne se doutait du travail que cela allait demander.
« Heureusement, nous sommes passionnés de technique et aucun membre de l'équipe n'a jamais baissé les bras même si nous avons plusieurs fois fait fausse route ou été confrontés à des obstacles inattendus », dit Håkan Carlberg, le chef de projet. « Les défis comme celui-ci sont très motivants, et personnellement j'étais convaincu que nous atteindrions notre objectif. »
Carlberg avait raison. En octobre 2019, Sandvik Coromant lancera la première référence d'un programme de 256 corps de forets CoroDrill DS20.
Le CoroDrill DS20 ressemble très peu à son prédécesseur plébiscité, CoroDrill 880. Au lieu de former une spirale à angle constant traditionnelle, les goujures du CoroDrill DS20 sont variables, commençant par une hélice et se poursuivant de manière rectiligne le long du corps du foret. C'est une des nombreuses caractéristiques sophistiquées développées pour optimiser les performances tout en favorisant la stabilité et l'équilibre des forces de cet outil long et asymétrique.
Chaque détail du CoroDrill DS20 a fait l'objet de longues recherches et autant de temps que nécessaire a été consacré à son développement. L'ingénieur de recherche Tomas Furucrona nous montre une petite plaquette dont l'optimisation a pris deux années. « Le premier grand défi a été de déterminer la bonne forme et le bon positionnement pour obtenir une force nette optimale étant donné que les deux plaquettes des forets sont positionnées de manière asymétrique. »
Le développement du corps du foret a été mené en parallèle par une équipe spécialisée qui a étudié, testé et analysé sa géométrie, son système d'arrosage et le matériau dans lequel il est fait pour trouver la combinaison idéale.
« Tout le monde peut fabriquer un foret de 7xD avec un diamètre spécifique », indique l'ingénieur de recherche et développement Fritz Alum Yah qui a planché sur le projet dès ses débuts. « Mais pour obtenir la même fiabilité avec un programme complet de diamètres de corps de forets, c'est une autre histoire. Nous avons dû développer de nouveaux modes de pensée et créer de nouvelles méthodes de calcul. »
Il y a eu de nombreux obstacles à surmonter. Les échecs lors des essais en laboratoire ont été nombreux. D'innombrables prototypes ont été détruits. Bien des idées ont été explorées puis abandonnées. Le défi posé par la forme des goujures et la présence des conduits internes d'adduction de liquide de coupe a demandé deux ans de travail pour trouver une solution. Et il y avait une cinquantaine d'autres paramètres à ajuster les uns aux autres. La modification d'un paramètre imposait de revoir les 49 autres.
« Nous avons su que nous allions dans la bonne direction quand notre ingénieur calcul Ramus Hemph, un scientifique talentueux, a développé une formule qui nous a donné la maîtrise de tous les paramètres », dit Carlberg. « Là où nous pensions en termes physiques, il voyait des chiffres et des vecteurs. La modélisation logicielle nous a permis de contrôler, moduler et analyser tous les paramètres de manière virtuelle. À partir de là, tout s'est mis en place. »
Malgré tout, de nouveaux défis sont apparus. Les capacités du CoroDrill DS20 ont été testées sur le terrain dans l'usine de SKF au Mexique où l'on produit des couronnes d'orientation pour éoliennes.
« En remplaçant le foret concurrent de 6xD par le CoroDrill DS20, les opérateurs de SKF ont été en mesure d'usiner tous les trous des pièces sans interruptions imprévisibles, sans problèmes et sans même à avoir à indexer les plaquettes », dit Furucrona. « La productivité a été doublée et les opérateurs étaient extrêmement satisfaits. »
Mais pour l'équipe de développement, il restait des détails à régler. « Nous avons dressé une liste de 15 problèmes, pour la plupart liés à la production, que nous allions devoir résoudre en 2 mois », dit Carlberg. « Nous y sommes parvenus. C'est dans notre ADN de toujours chercher plus loin pour parfaire les nouvelles solutions et les innovations. »
Le développement du CoroDrill DS20 a été un travail collaboratif international. Le gros de l'équipe était basé à Sandviken, mais elle était secondée par plus de 50 personnes situées à Gimo et Västberga en Suède, ainsi qu'à Mebane aux États-Unis.
Forets CoroDrill® DS20 - Sept années de développement
SANDVIK COROMANT
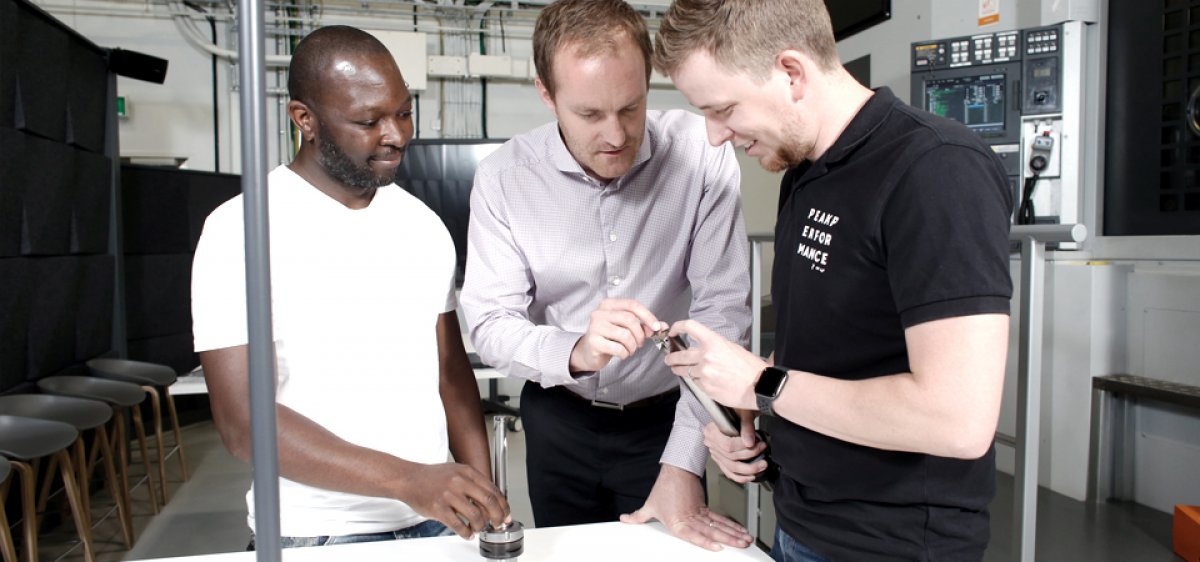
Recherches associées à Matériaux, Outillage, Composants
Dernières actualités ajoutées parInfoWeb Marketplace
Bollé Safety
Bollé Safety remporte le prix "Product Design" au "Red Dot Design Award"
Lire le communiquéYaskawa